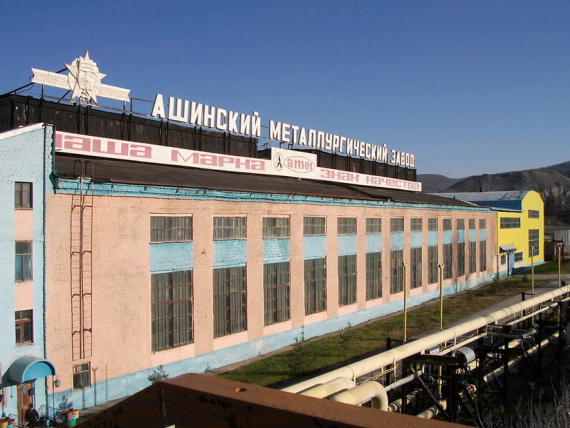
Металлургическая отрасль весьма динамична в своем развитии, доля чёрной металлургии в объёме промышленного производства России составляет около 10 %. В сфере чёрной металлургии работают более 1500 предприятий, 70 % из них — градообразующие, число занятых — работников более 660 000 человек. Тем сильнее потери экономики вследствие неэффективных технологических и производственных процессов на предприятиях.
На настоящий момент на предприятиях отрасли черной металлургии широко распространены следующие проблемы:
1. Неэффективное расходование материально-технических ресурсов (электроэнергия, шлакообразующие и легирующие материалы, шихта, аргон и тд).
2. Отсутствие техобслуживания и ремонта основного оборудования по состоянию (распространены планово-предупредительные ремонты), что приводит к недоутилизации ресурса оборудования или, наоборот, к авариям вследствие нарушения технологии.
3. Высокое влияние человеческого фактора на результат исполнения технологических инструкций, что приводит к нестабильному качеству продукции.
Проблемы не новы и даже не специфичны для черной металлургии, и часто применимы точечные решения через повышение трудовой дисциплины на конкретном участке. К сожалению, дисциплине всегда противостоит человеческий фактор, поэтому тренд последних лет – системно решать подобные задачи с помощью технологий Индустрии 4.0. Предприятия черной металлургии, как, впрочем, и другие промышленные предприятия, активно создают проектные офисы Индустрии 4.0, вводят в штатное расписание должности директоров по инновациям, реализуют программы по цифровизации, повышению горизонтальной и вертикальной интеграции информационных систем и внедрению инструментов Искусственного интеллекта (ИИ). Некоторым предприятиям, причем, даже удается добиваться заметного экономического эффекта от этих преобразований.
Ожидаемо, в признанных отраслевых лидерах тренда Индустрии 4.0 находятся крупнейшие комбинаты, такие как Северсталь, Магнитогорский металлургический комбинат и НЛМК, но перспективность использования новых технологий становится очевидна и небольшим заводам. Тем более, что вопрос цифровизации и повышения эффективности в настоящем конкурентном рынке это уже не роскошь, а средство выживания, и все, что ты не сэкономил – ты потратил. Для публичных акционерных обществ пресс-релизы о принятии и утверждении стратегии Индустрии 4.0 являются важным сигналом рынку и акционерам об инвестиционной привлекательности предприятия.
ПАО «Ашинский металлургический завод» в этом году провёл успешное пробное испытание интеллектуальной системы, которая позволяет снизить себестоимость продукции.
Ашинский металлургический завод по металлургическим меркам предприятие относительно небольшое, выпускает 650 000 тонн стали, на нем работают 4500 человек. Однако это компактное производство входит в 5-ку лучших поставщиков толстолистового проката из углеродистых, низколегированных, конструкционных и легированных марок стали.
Одной из стратегических задач завода является повышение конкурентоспособности за счет снижения себестоимости стали. Себестоимость складывается из более чем 20-и статей затрат, таких как: металлошихта – сырье и ферросплавы, отходы и брак, расходы по переделу – электроэнергия, природный газ, электроды, зарплата сотрудников предприятия и др.
Для общего понимания хотелось бы отметить, что одной из основных статей в структуре затрат сталеплавильного производства являются ферросплавы. Они используются для раскисления и легирования стали. В зависимости от марки стали и сортамента эти затраты могут составлять от 3 до 10% общей стоимости материальных затрат.
Сергей Костромцов, начальник отдела АСУ ТП ПАО «Ашинский металлургический завод» рассказал, как они решали одну из задач по оптимизации расхода ферросплавов на участке внепечной обработки.
«В решении таких амбициозных задач важную роль играет сотрудничество с надежным партнером, имеющим необходимые компетенции в данной области. Таким партнером для нас стала компания Datana, совместно с которой мы внедрили пилотное решение, которое показало нам перспективу сокращения издержек производства за счёт снижения расхода ферросплавов. Система может производить расчет отдачи ферросплавов с наименьшей стоимостью, при этом соблюдая все технологические условия и физико-химические параметры конечной продукции. В режиме реального времени наши сталевары получают рекомендации, как эффективнее вести процесс выплавки стали.
В основе решения лежит математическая модель, которая базируется на физико-химических закономерностях, тепло- и массообменных процессов между существующими фазами (газ-шлак-металл) и алгоритмах машинного обучения.
На протяжении 3 недель испытаний, мы провели десятки плавок, в результате чего была доказана возможность получения положительного экономического эффекта в виде снижения удельного расхода ферросплавов для стали марки Ст3сп на 3-6%. Если переводить это в деньги, то экономический эффект от внедрения такого решения поможет сэкономить предприятию немалые средства».
Внедрение технологических инноваций в промышленности в общем, и в частности в металлургии, реализация новых бизнес-моделей поддерживается и стимулируется в России на государственном уровне. “Цифровизация промышленности – это объективное настоящее и даже успешное прошлое для многих зарубежных предприятий, поэтому интерес к внедрению цифровых технологий закономерно набирает обороты среди российских предприятий самых разных отраслей. Любой промышленник, желающий удержаться на плаву и даже укрепить свое положение на рынке, стремится быть в курсе этих процессов, он заинтересован воспользоваться конкурентными преимуществами, которые можно выиграть от цифровизации производства. В долгосрочной перспективе – это вопрос выживания предприятия”, - считает министр промышленности и торговли РФ Денис Мантуров. Руководству же промышленных предприятий необходимо понимать, что никакая поддержка государства не заменит личной вовлеченности ТОП-менеджмента в решение задач цифровизации. В противном случае, вся инновационная деятельность дальше пилотных проектов не пойдет.